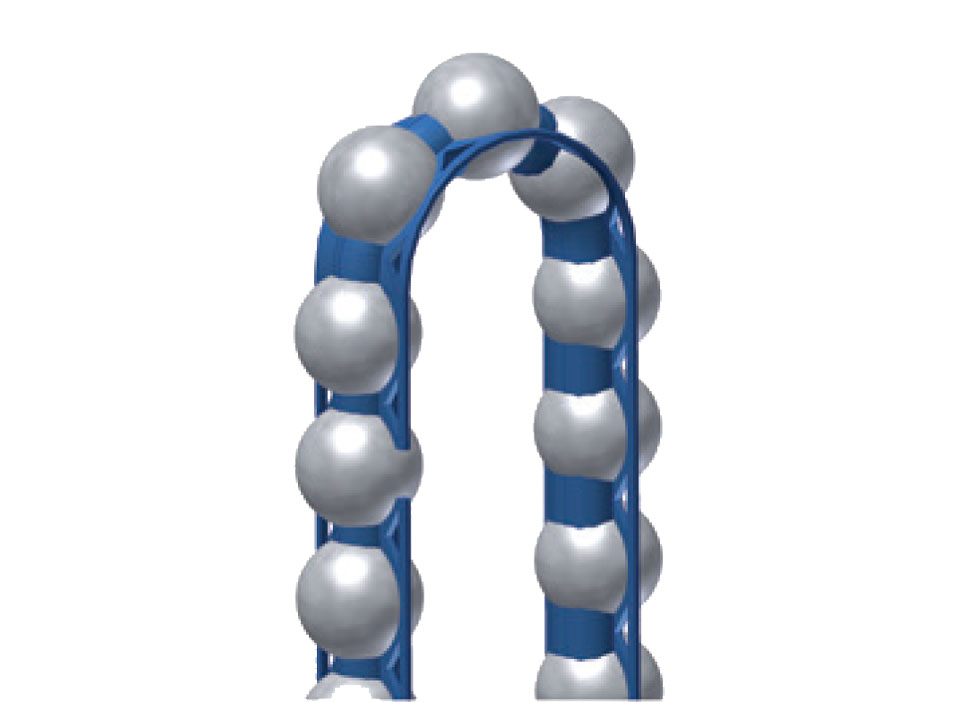
Should You Consider Caged Linear Guides?
Conventional linear guides have been used in industry for a wide range of applications. They can transport large loads in a compact package and meet the accuracy and repeatability requirements of even the most demanding applications. What if you could take that capability to the next level and increase bearing life, reduce noise, and also be more efficient with your lubrication maintenance schedule and do it in the same compact package?
Cages for guiding the rolling elements of bearings have been used for over 100 years but did you know they are also part of the newly developed linear guides?
The rotating balls in conventional guides have point contact between each other (Figure 1.6). The rotational speed at the contact point is double that of the linear speed of the balls and the contact area (A) is so small that the surface pressure (P) pushes towards infinity. This pressure can cause heat and wear of the balls and the linear guide system. The cage in caged linear guides acts as a retainer preventing contact between the balls (Figure 1.6). Additionally, the ball and cage have a larger contact area (A) than the point contact in conventional guides. This reduces the surface pressure (P) leading to less heat generation and longer life.
Conventional linear guides allow contact between the balls during operation, which may lead to increased lubricant consumption, higher friction, noise and heat. Caged linear guides work to minimize all of these effects.
In addition, the contact of the balls with the surfaces of the recirculation path affects noise generation (Figure 1.8). The use of cages significantly reduces these effects. The patented structure of the NTN’s cages contains gaps for lubrication storage. Combined with the structural flexibility of the cage, noise levels are reduced.
With conventional linear guides it is not possible to keep the distance of the balls (C1, C2) constant (Figure 1.8). With the addition of a cage for the balls this distance is able to be held constant, making for increased smoothness when running.
At the same time, the balls are continuously supplied with lubricant, which reduces wear of the metal. This significantly extends the service life of the lubricant and the maintenance intervals.
Thinking of using caged linear rails in your next application? Do you already have NTN profile rails and are considering moving toward caged runner blocks? With NTN’s “One Rail For All” technology both conventional and caged runner blocks can run on the same rail, meaning no reassembly of the guide rails in changeover situations.
PDF Tech Tip: Click Here
Author: Jon Kasberg