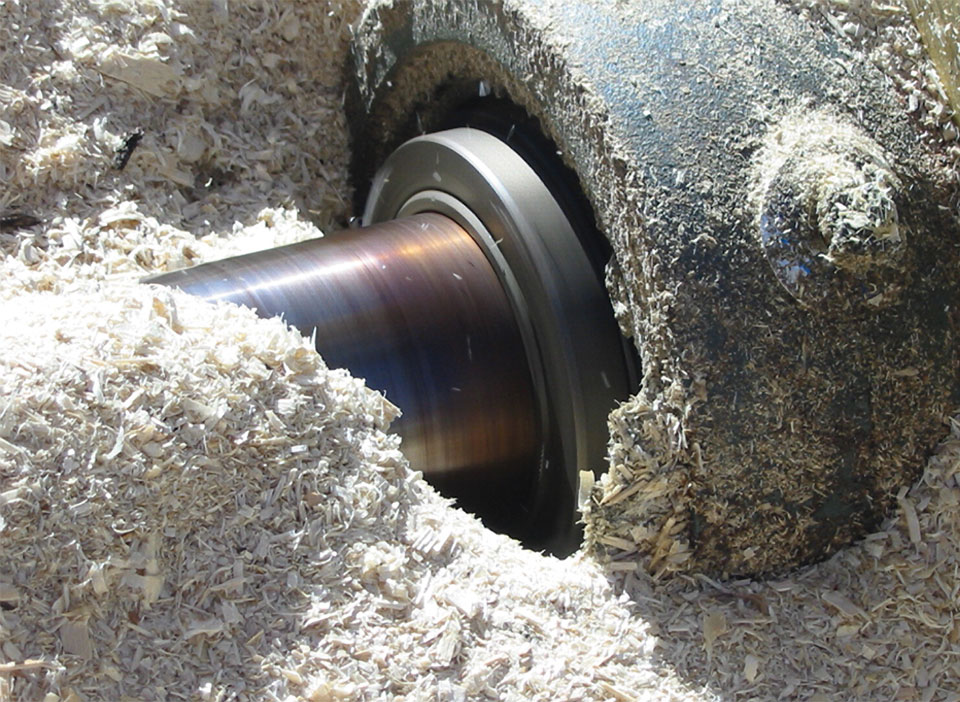
Adding Grease to Housing Covers Helps Prevent Contamination
Outdoor conveyor systems see some of the harshest environments of any bearing application. These conveyor systems commonly use heavy-duty spherical roller bearing SAF mounted units, utilizing split cast iron housings and various seal configurations. Even with all of the exotic seal configurations, these heavy-duty bearing units still see damage resulting from either environmental or application contamination. In the application, the build-up of the transported material on the bearing face (Fig. 1) will eventually lead to seal wear and contamination ingress. Once the contamination gets into the bearing it is only a matter of time before failure occurs.
One way NTN has helped is with the development of the sealed SPAW heavy-duty mounted unit. The SPAW, a drop in replacement for SAF units, has integrated spring-loaded seals to the bearing (Fig. 2), a ductile unitized housing, phosphate coated bearing and adapter sleeve, as well as the options for open and closed covers. NTN has seen great success with this bearing is in conveyor applications utilizing the covers and adding grease in the cavity between the bearing and the cover (Fig. 3). The grease dam acts as a trap for contamination, thus preventing it from reaching the bearing seal face. Keeping contaminants out of the bearing will lead to longer bearing life and reduced downtime, meaning a cost savings to the customer.
PDF Tech Tip: Click Here
Author: Roberto Carriedo